Economia
Acciaio “Green” ed economico? L’elettrochimica ha la soluzione
Si pul ricavare il ferro sena utilizzare carbone e altoforni, in mdo economicamente conveniente? Si , grazie all’elettrochimica, all’acqua marina e al sale, ottenendo ferro purissimo e cloro
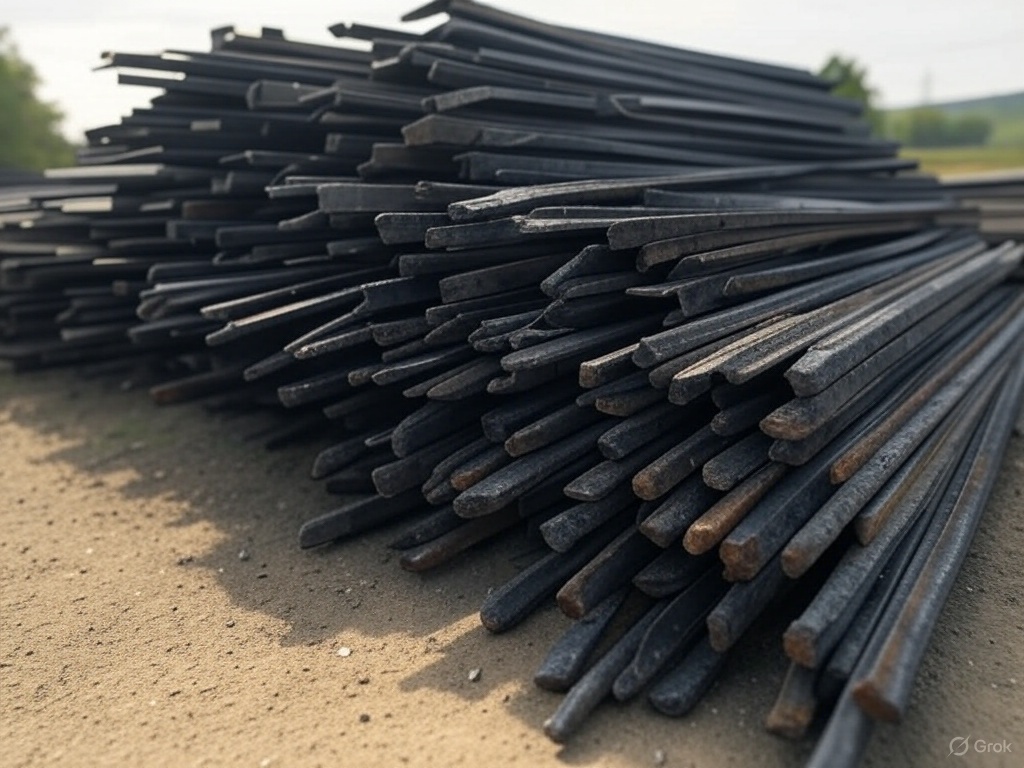
L’acciaio rappresenta la spina dorsale della civiltà moderna, trovando impiego in svariati settori, dagli edifici ai ponti, dalle automobili agli elettrodomestici. Tuttavia, la sua produzione si configura come una delle principali fonti di emissioni di carbonio a livello globale, in particolare a causa del tradizionale processo di estrazione del ferro dal minerale tramite altiforni alimentati a carbone.
Considerando la continua crescita della domanda globale di acciaio, l’individuazione di metodi di produzione più puliti e sostenibili riveste un’importanza cruciale, non solo per il raggiungimento degli obiettivi climatici, ma per il futuro stesso dell’industria siderurgica.
Attualmente, i ricercatori stanno esplorando l’elettrochimica come approccio innovativo per trasformare il processo di produzione del ferro, l’elemento Si chiave dell’acciaio. Invece di ricorrere a forni ad alta temperatura alimentati con combustibili fossili, questo metodo emergente sfrutta l’elettricità per estrarre ferro puro dall’ossido di ferro a temperature significativamente inferiori e con emissioni notevolmente ridotte.
Questo rappresenta un promettente passo avanti verso un’industria siderurgica più ecologica, capace di contribuire alla riduzione dell’inquinamento senza compromettere le prestazioni o la redditività.
Ripensare il minerale di ferro su scala industriale
Presso l’Università dell’Oregon, il chimico Paul Kempler e il suo team sono impegnati nello sviluppo di un processo elettrochimico in grado di convertire ossido di ferro e acqua salata in ferro metallico puro, generando contestualmente cloro, un sottoprodotto di valore commerciale.
Questo metodo potrebbe attenuare l’impatto ambientale della produzione tradizionale di ferro e, in prospettiva, competere in termini di costi con gli attuali approcci basati sull’utilizzo del carbonio.
Nel corso dell’anno precedente, il team ha dimostrato con successo, a livello di laboratorio, la capacità dell’elettrochimica di convertire l’ossido di ferro in ferro.
Tuttavia, i minerali di ferro presenti in natura presentano una complessità maggiore rispetto ai materiali purificati impiegati nei test iniziali. Per avvicinare il loro processo alla realtà industriale, i ricercatori hanno dovuto analizzare quali tipologie di ossidi di ferro naturali si sarebbero dimostrate più efficaci in queste reazioni a bassa temperatura.
“Abbiamo un principio chimico, una sorta di regola di progettazione, che ci guiderà nell’identificazione degli ossidi di ferro a basso costo che potremmo impiegare in questi reattori”, ha spiegato Kempler.
La forma vince sulle dimensioni!
Per rispondere a questa cruciale domanda, la ricercatrice post-dottorato Ana Konovalova e lo studente laureato Andrew Goldman hanno condotto uno studio approfondito sull’influenza della forma e della struttura delle particelle di ossido di ferro sul processo elettrochimico.
Hanno creato particelle sia porose che dense, caratterizzate da composizioni simili ma con un’architettura interna differente.
I risultati ottenuti sono stati inequivocabili: la porosità gioca un ruolo determinante. Le particelle porose, grazie alla loro maggiore superficie interna, consentono una produzione di ferro più rapida ed efficiente. Al contrario, le particelle dense hanno rallentato il processo e limitato la quantità di ferro producibile in una singola operazione.
“Con le particelle altamente porose, possiamo produrre ferro molto rapidamente su una piccola area”, ha affermato Goldman. “Le particelle dense non riescono a raggiungere la stessa velocità, limitando quindi la quantità di ferro che possiamo produrre per metro quadrato di elettrodi”.
Un grande balzo in avanti
L’efficienza non rappresenta solamente un successo scientifico, ma costituisce una necessità commerciale. Gli impianti elettrochimici su larga scala comportano investimenti significativi, e la rapidità con cui un sistema è in grado di produrre ferro incide direttamente sul suo ritorno economico.
Sfruttando particelle porose, il team ha stimato di poter produrre ferro a un costo inferiore a 600 dollari per tonnellata metrica, un livello competitivo con la produzione convenzionale. Ulteriori progressi nella progettazione degli elettrodi e dei materiali porosi potrebbero potenzialmente ottimizzare ulteriormente il processo.
Per accelerare la transizione dal laboratorio all’applicazione industriale, il team sta collaborando attivamente con ingegneri civili dell’Oregon State University e con un’azienda specializzata nella produzione di elettrodi.
“Credo che questo lavoro dimostri che la tecnologia può soddisfare le esigenze di una società industriale senza arrecare danni devastanti all’ambiente”, ha dichiarato Goldman. “Naturalmente, non abbiamo ancora risolto tutte le problematiche, ma ritengo che questo rappresenti un esempio che funge da punto di partenza per un approccio differente alle soluzioni”.
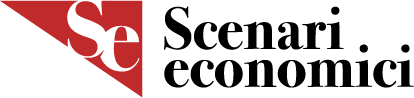
You must be logged in to post a comment Login